Lime putty is essentially liquefied limestone, ready to be used as a natural binder for a wide variety of plastering and masonry mortars and paints. Since early human history, lime putty has played a fundamental role in architectural development, enabling the creation of durable, breathable structures that stand the test of time. Its unique properties make it a sustainable choice that continues to support and inspire modern building practices.
Lime Putty, Liquid Stone
Limestone forms over millions of years as the shells and skeletons of tiny sea creatures accumulate on the ocean floor. These layers are gradually compressed and cemented together, turning into a whitish, solid rock through natural processes.
When limestone is heated and then immersed in water, it transforms into a liquid-like material that is easy to apply and, once dried, gradually returns to its original solid state. This ancient process, first described by Vitruvius around 40 BC and refined with modern technology, provides the ideal material for our lime plasters.
Producing high-quality lime mortars, plasters, and paints requires an understanding of how the manufacturing process shapes the lime’s qualities. Lime putty mortars harden by absorbing CO₂, transforming back into their original limestone form, a process known as the Lime Cycle, which gives lime-based materials their unique properties.
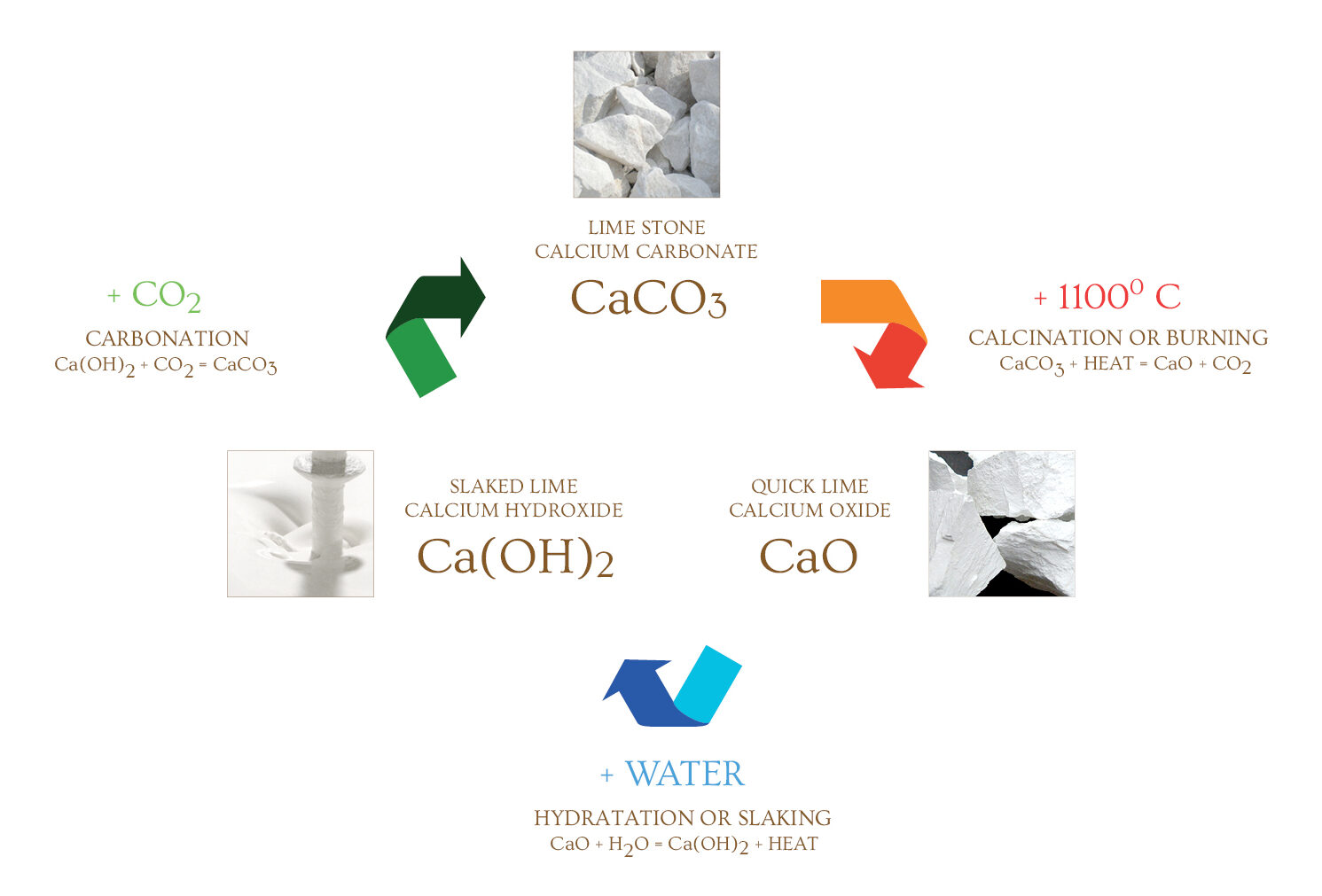
The lime cycle
Calcination: After the limestone is quarried and crushed, the stone is heated to produce quicklime.
Slaking: the quicklime is immersed in an abundance of water and aged for a significant amount of time.
Carbonitation: the lime putty dries and absorbs carbon dioxide from the air, returning to its original limestone form.
Calcination: Turning Limestone into Quicklime
CaCO₃(s) + HEAT → CaO(s) + CO₂(g)
To transform calcium carbonate (CaCO₃) into calcium oxide (CaO), known as quicklime, limestone must be heated to around 1,000 degrees Celsius in a process called calcination. This intense heat causes the limestone to release carbon dioxide (CO₂), resulting in a highly reactive material.
The physical characteristics of the resulting quicklime, such as porosity, density, and reactivity, are directly influenced by the purity of the raw limestone. High-purity limestone produces a more consistent and reactive quicklime, enhancing the material’s ability to bond and strengthening its performance in building applications. Lower-purity limestone, on the other hand, may result in a denser, less porous quicklime, which can affect the mortar’s workability and strength.
Slaking: Liquifying the quicklime
CaO(s) + H₂O(l) → Ca(OH)₂
After calcination, calcium oxide (quicklime) must undergo a process called slaking to produce a high-quality air lime binder. This involves immersing the quicklime in three times its volume of water, which causes a chemical reaction that transforms it into calcium hydroxide (Ca(OH)₂), a smooth, creamy putty, the base material for air lime mortars and paints.
The Aging Process
During the crucial aging phase, the microscopic calcite crystals in lime putty undergo a transformation, breaking down into nanometer-scale particles that arrange themselves into layered, laminated structures filled with molecular water. This process forms a fine microcrystalline structure that is essential for high-quality lime-based materials.
The aging precess significantly impacts the properties of the final product, enhancing its ductility, breathability, elasticity, and mechanical strength. Extended storage of slaked lime putty not only improves these qualities but also increases the durability and workability of the lime mortar, resulting in a superior building material.
Carbonatation: returning to stone
Ca(OH)₂ + CO₂ → CaCO₃ + H₂O
As a mortar made from aged lime putty and sand begins to dry, it undergoes a transformation from calcium hydroxide back to calcium carbonate by losing water and absorbing CO₂ from the atmosphere. This process, known as carbonatation, gradually returns the material to a stone-like state. The older the lime putty used, the faster and more complete the carbonatation, enhancing the mortar’s final strength.
As water evaporates from within the mortar, tiny channels form, giving it natural breathability and elasticity to adapt to slight structural movements. Additionally, the fine microcrystalline structure developed during aging further reinforces the plaster, providing it with outstanding mechanical resistance and long-term durability in various building applications.
Quality: What to watch out for
Powdered Hydrated Lime
An industrial method involves crushing quicklime and misting it with water to produce powdered hydrated lime, which is easier to transport without added water. However, this partial slaking process results in weaker bonds in the final product, leading to cracks and micro-fissures. High-quality hydrated lime is always applied as a liquid paste in the second stage of the lime cycle.
Fake Slaking
Some producers rehydrate powdered lime to create a paste-like texture. However, this lime has already undergone partial carbonation, meaning many particles have absorbed CO₂ and won’t contribute to proper bonding. This results in a weaker, less durable plaster or mortar.
Marginally Hydraulic Lime
Lime from certain quarries may contain impurities, making it slightly hydraulic. Although it binds well, marginally hydraulic lime is less breathable and flexible than pure non-hydraulic lime, changing the properties of the mix.
Artisan Stucco Original Lime Putty
Our lime putty is crafted with care, using high-quality limestone from Northern Spain and an extended, meticulous production process to ensure durability, workability, and a refined finish.
Premium Limestone Source
We source limestone from the Ebro basin in Northern Spain, chosen for its bright white color and high calcium content, which enhances the purity of our lime.
Six-Month Slaking Process
After heating, the limestone is slaked in water for a minimum of six months, allowing it to fully transform into a smooth, stable paste with 97% liquefied calcium carbonate.
Fine Structure
The stone undergoes careful crushing and sieving, resulting in a fine microcrystalline structure that boosts elasticity, breathability, and mechanical strength.
Customized Blending
We mix our lime putty with marble sands and mineral pigments in precise proportions to achieve the exact color, texture, and performance needed for each project.
Our attention to the details of the process ensures that Artisan Stucco Original Lime Putty meets the highest standards, delivering lasting quality and beauty. This excellent material forms the basis for all our Lime Putty based products, such as our Lime Paints and Lime Plaster Materials.
Bibliography
C. Rodríguez Navarro, Eric Hansen, William S. Ginell
Calcium Hydroxide Crystal Evolution upon Aging of Lime Putty.
J. Am. Ceram. Soc. 81 [11] 3032-34 (1998)
Eric E. Hansen, C. Rodríguez Navarro, Koenraad Van Balen
Lime Putties and Mortars. Insights into fundamental properties
Studies in conservation 53 (2008) pages 9-23
Olga Cazalla, C. Rodríguez Navarro, Eduardo Sebastian, Giussepe Cultrone
Aging of Lime Putty: Effects on Traditional Lime Mortar Carbonatation
J. Am. Ceram. Soc. 83 [5] 1070-76 (2000)
C. Rodríguez Navarro, E. Ruiz Agudo, M. Ortega Huertas E. Hansen
Nanostructure and Irreversible Colloidal Behavior of Ca(OH)2: Implications in Cultural Heritage Conservation.
Langmuir 2005, 21, 10948 – 10957
Sonia Argano, Monserrat Guixeras
Cal Aérea en Pasta: Apuntes para su buen uso
ISBN 8461355954, 9788461355952
Publisher: Joystuc 2009
Ian Brocklebank
The lime spectrum
Building Limes Forum. Context 97: November 2006